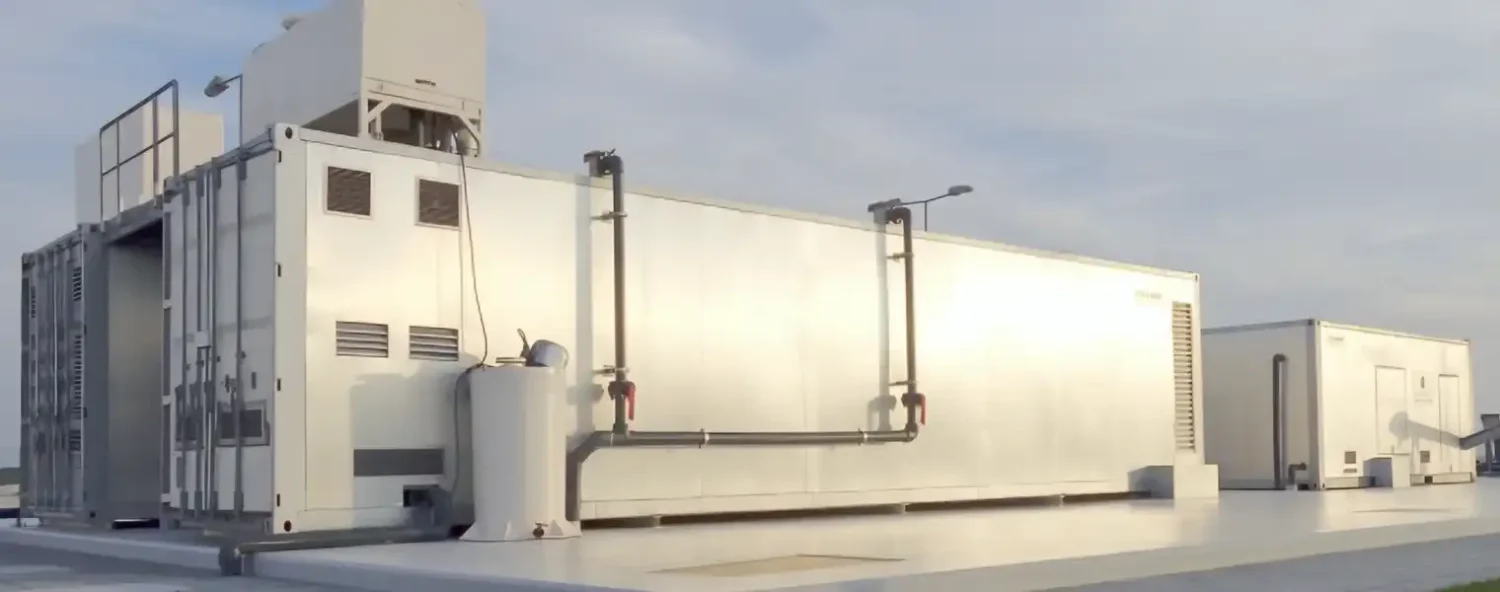
Membrane Bioreactors (MBR)
Advanced MBR Systems for Efficient Industrial Wastewater Treatment
Hydroflux offers high performance Membrane Bioreactor (MBR) technology for the efficient treatment of wastewater across various industries. Combining the benefits of activated sludge and membrane filtration, our MBR systems provide superior effluent quality, reduced footprint, and lower operational costs. With years of experience and a focus on innovative and sustainable solutions, Hydroflux ensures that your wastewater treatment needs are met with reliability, precision, and long-term performance. Some of the industry sectors we work with include:
- Meat and Poultry
- Dairies
- Beverage sector
- Fruit and vegetable processing
- Potato and potato chips
- Vegetable oil processing
- General Food industry
- Manufacturing
- Industrial laundries
- Paper, cardboard and printing
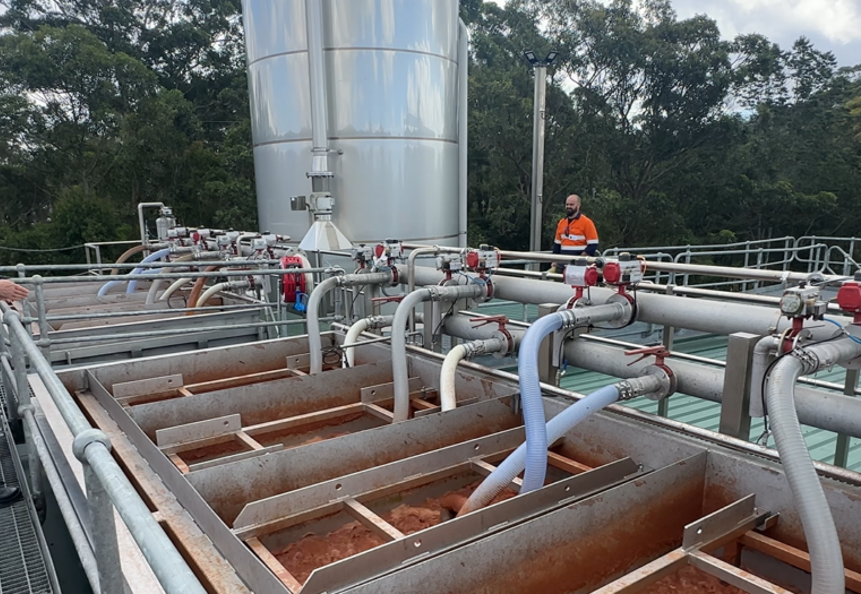
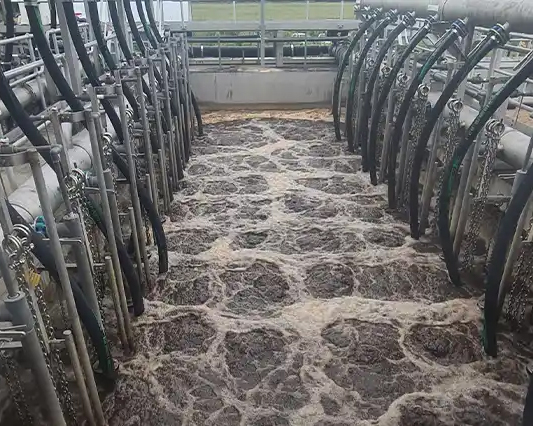
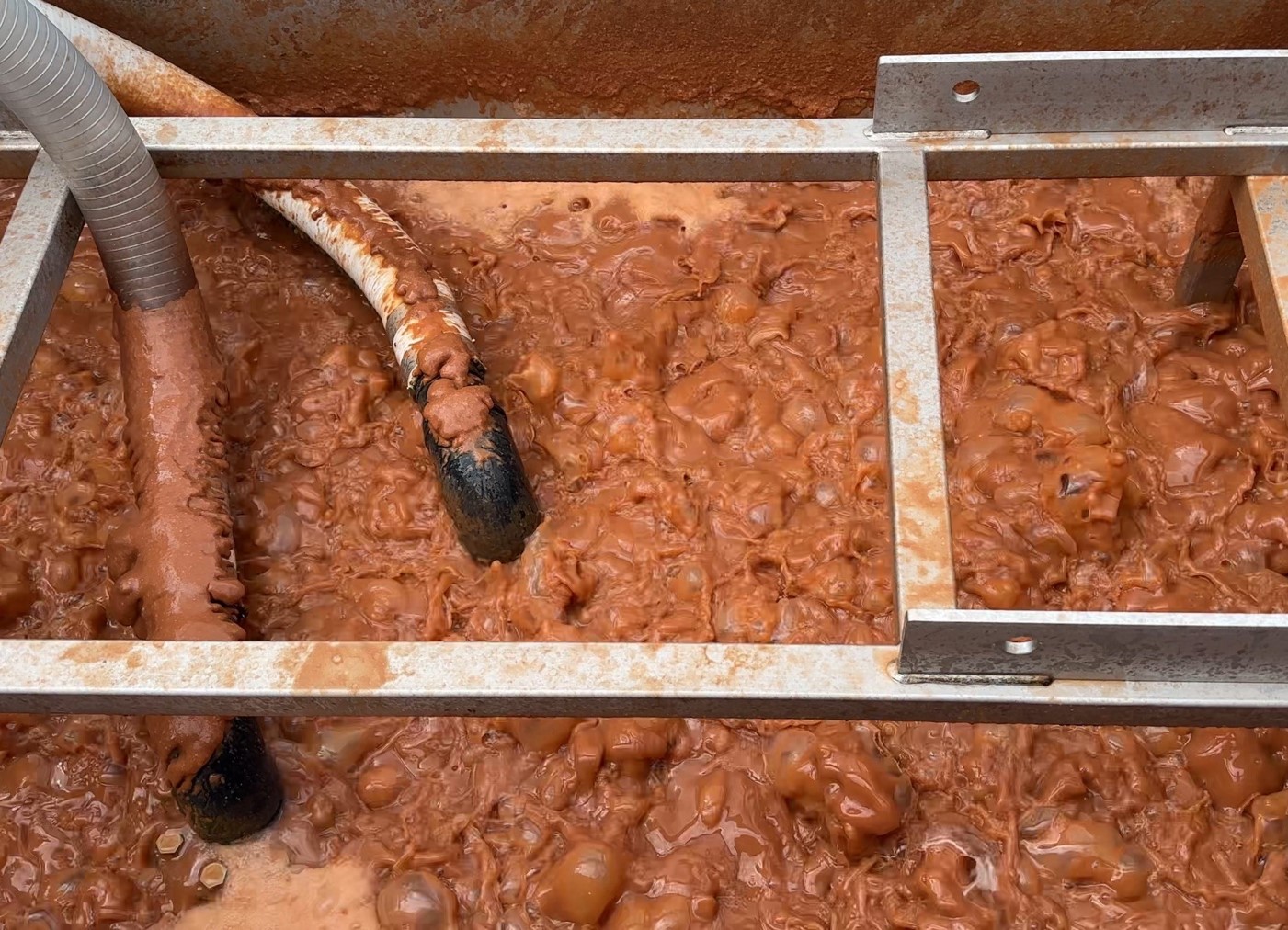
The main benefits of MBR technology over other aerobic processes are:
- The production of a very high-quality treated water due to the use of membranes for separating biomass from the treated wastewater stream.
- This high-quality permeate enables treated water to be used directly for non potable reuse or further treated in RO systems for direct potable reuse
- The MBR requires a comparatively small aerobic tank footprint due to elevated mixed liquor suspended solids (MLSS) operating concentrations
How the MBR Works
The MBR process is an aerobic treatment system incorporating an aeration zone followed by removal of biomass via membrane filtration. The use of membranes as the separation method provides ultimate water quality by having a definitive barrier for solids removal.
The Stages of the MBR Process
- Wastewater is introduced into the aeration tank at a constant flow rate where oxygen is introduced
- Biologically treated wastewater flows out of the aeration tank directly into the membrane tank
- Water is pumped from the tank via the membranes to the point of discharge
- Biomass is periodically removed from the membrane tank and is dewatered and further processed, or removed from site as waste activated sludge (WAS). Some biomass is returned back to the aeration tank to retain suitable mixed liquor suspended solids (MLSS) levels
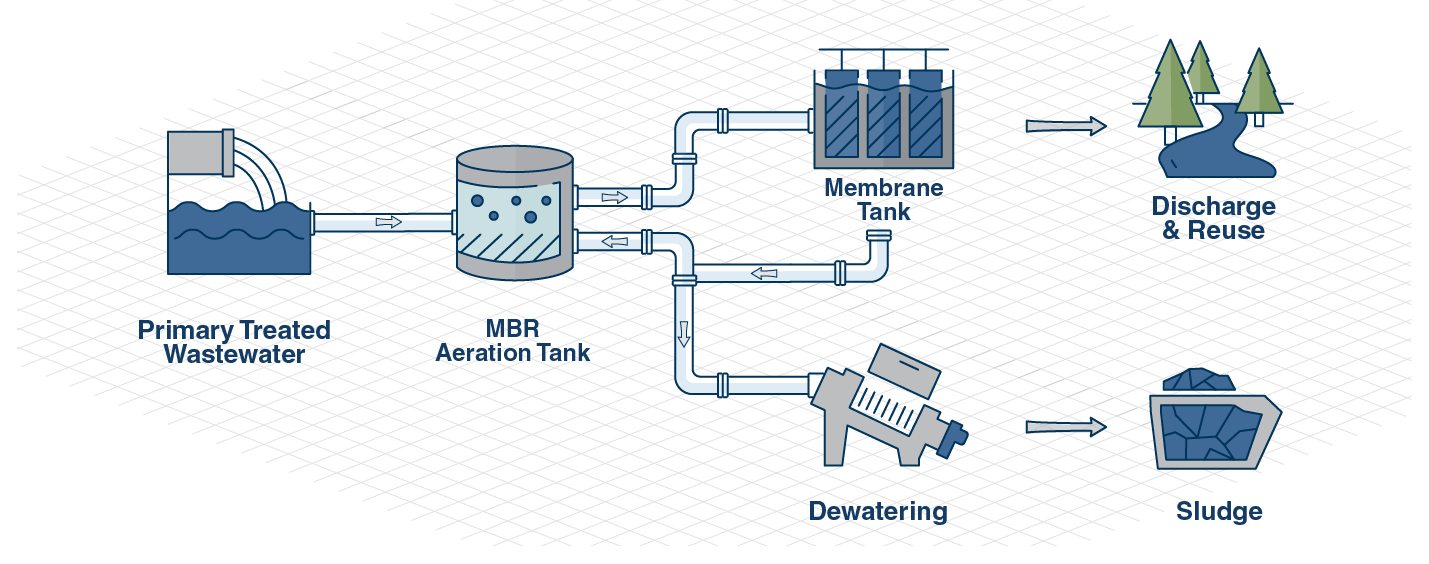
Nutrient removal
Nitrogen removal can be incorporated into the MBR process by the inclusion of an anoxic zone upstream of the aeration tank with a mixed liquor return (MLR) loop that recirculates water between the aeration and anoxic tanks. Some phosphorous will be taken up in the biological process however if very low concentrations are required, a simple addition of coagulant into the reactor is possible to chemically precipitate phosphorous.
Why Choose Hydroflux for Your MBR System Construction?
Unmatched Quality: At Hydroflux, we are committed to delivering high quality MBR systems with exceptional build quality. We ensure that every system is built to last and operates with maximum efficiency, ensuring long-term performance and reliability.
Proprietary Equipment for Superior Results: Hydroflux utilies proprietary ancillary equipment such as the HyDAF and Huber Screw Press to compliment the overall MBR process. These advanced systems work synergistically with the MBBR process, ensuring appropriate primary treatment and efficient sludge removal which improve solids separation, and reduce operational costs.
Choosing Hydroflux means selecting a trusted partner that combines high-quality systems, specialised equipment, and deep industry expertise to deliver outstanding wastewater treatment solutions.
MBR FAQs
In Membrane Bioreactor (MBR) systems, flat sheet and hollow fiber (tube) membranes are the two primary configurations used. Flat sheet membranes are usually employed by Hydroflux are arranged in a rack configuration which offers a large surface area for filtration enhancing filtration efficiency and reducing membrane fouling. Hollow fiber membranes, which consist of small, tube-like fibers, are usually more compact and often employed in inside-out filtration. These membranes offer a more space-efficient solution and incur lower capital costs, though they are more susceptible to fouling due to the smaller flow channels within the fibers. Hydroflux can supply either flat sheet or hollow fiber membrane in its MBR designs.
Hydroflux uses world-leading technology from recognised membrane manufacturers for their MBR systems, ensuring the highest quality and performance in wastewater treatment. By partnering with renowned leading membrane manufacturers, Hydroflux guarantees that their MBR systems deliver superior filtration efficiency, durability, and long-term reliability. Additionally, these partnerships ensure the availability of local spare parts and service, making maintenance and support more accessible.
Membrane Bioreactors (MBRs) offer significant advantages over conventional activated sludge systems in wastewater treatment, primarily due to the integration of the actual membrane filtration process. MBR systems produce higher-quality effluent, as the membrane acts as a physical barrier to suspended solids, achieving more efficient removal of biomass and reducing pathogens that conventional or “non-membrane” systems cannot do. Additionally, MBRs have a more compact footprint, particularly when combining biological treatment and filtration in one process, which saves space and reduces infrastructure requirements. The high biomass concentration in MBRs also enables them to handle variable flow rates and organic loads more effectively, offering greater flexibility and performance under fluctuating conditions.
While MBRs traditionally may have had a higher energy consumption than alternative aerobic wastewater treatment systems due to the filtration process and the additional energy required for scouring, advancements in technology have improved their energy efficiency, making them comparable especially when factoring in the reduced need for additional equipment such as clarifiers.
Overall, MBRs provide superior operational control, effluent quality, and space efficiency, making them ideal for modern wastewater treatment needs in industries with stringent discharge standards or limited space.
The maintenance requirements for a Membrane Bioreactor (MBR) system primarily focus on the membrane filtration components. Over time, membranes can experience fouling, which reduces filtration efficiency and may lead to increased energy consumption. To mitigate fouling, regular cleaning is necessary. This typically involves chemically cleaning the membranes using acidic or alkaline solutions to remove accumulated organic and inorganic matter. The frequency of cleaning depends on the wastewater characteristics and operational conditions but is typically performed every few weeks or months. Additionally, membrane integrity should be regularly checked, and any damaged membranes should be replaced to maintain optimal performance.
Design and Construction Capabilities
Hydroflux has the expertise and capability to deliver design-and-construct project and offers flexible contract options, ranging from equipment design and supply to full turnkey installations.
With a team of qualified civil, mechanical, chemical, and electrical engineers, as well as experienced project managers, site supervisors, commissioning engineers, and service technicians, Hydroflux ensures expert execution at every stage. Our offices across Australia provide a strong local presence, ensuring seamless project management from design through to installation. Additionally, Hydroflux offers post-installation routine service contracts to maintain system performance and longevity.
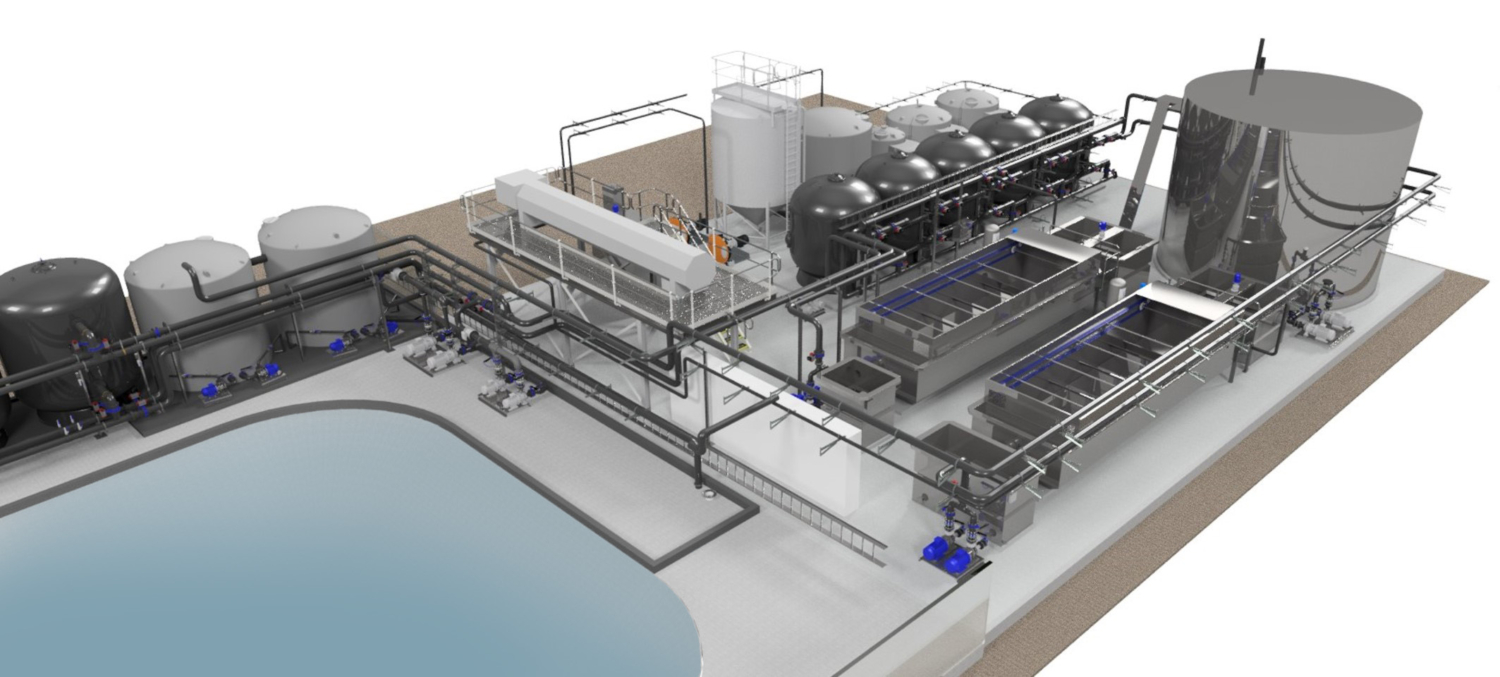
Sustainable Solutions
As Australia’s first certified carbon-neutral water and wastewater chemical supply and service business, we focus on sustainability. Developing and delivering sustainable solutions for treatment plant operation and maintenance is at the core of what we do. Our equipment is the most sustainable in the Australian and New Zealand market and is also carbon-neutral. Click here to find out what this means for you.
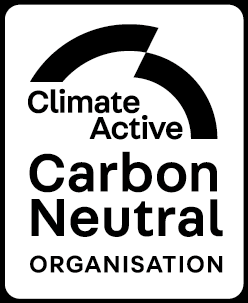