VeeMax® Sludge Clarifier Thickener for Image Flat WTP
The Image Flat Water Treatment Plant feeds Nambour, Yandina, Eumundi and coastal urban development north of the Maroochy River in Queensland.
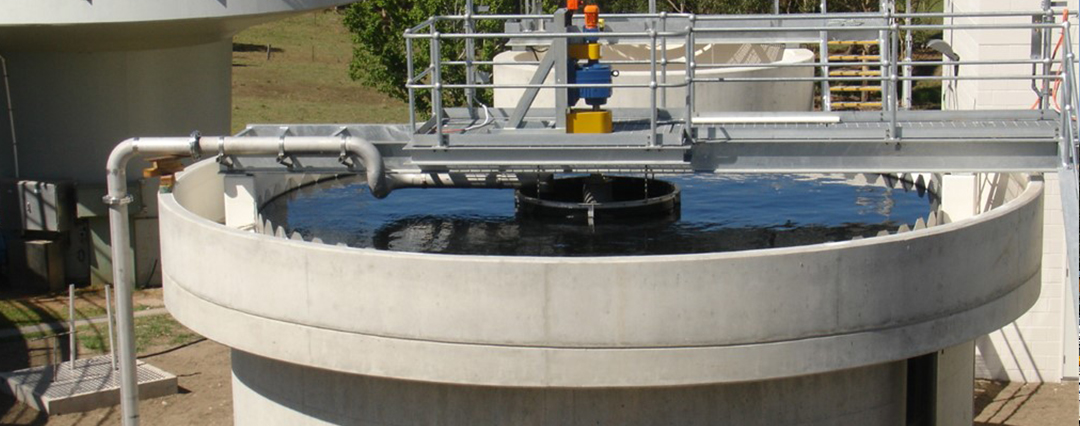
Project Overview
Image Flat WTP was upgraded in 2014 to increase capacity and the works include the installation of a new clarifier thickener for backwash water recovery. A Hydroflux Epco VeeMax® Clarifier Thickener was installed into an above ground concrete tank.
The unit is driven by a reduction gear motor. The scraper runs continuously and is protected by a torque limiter. In operation, the feed enters the tank through the inlet pipe that discharges into the feedwell.
Any high inflow currents are contained by the feedwell, which forces the flow downward toward the bottom of the tank. The settleable material deposits on the floor with the major concentration towards the centre of the tank.
The sludge is collected by the scraper blades by their rotation, and is moved across the floor to the sludge hopper in the centre of the tank by the floor slope and the blade pattern. Clarified effluent leaves the tank via the peripheral vee notched weir plates.
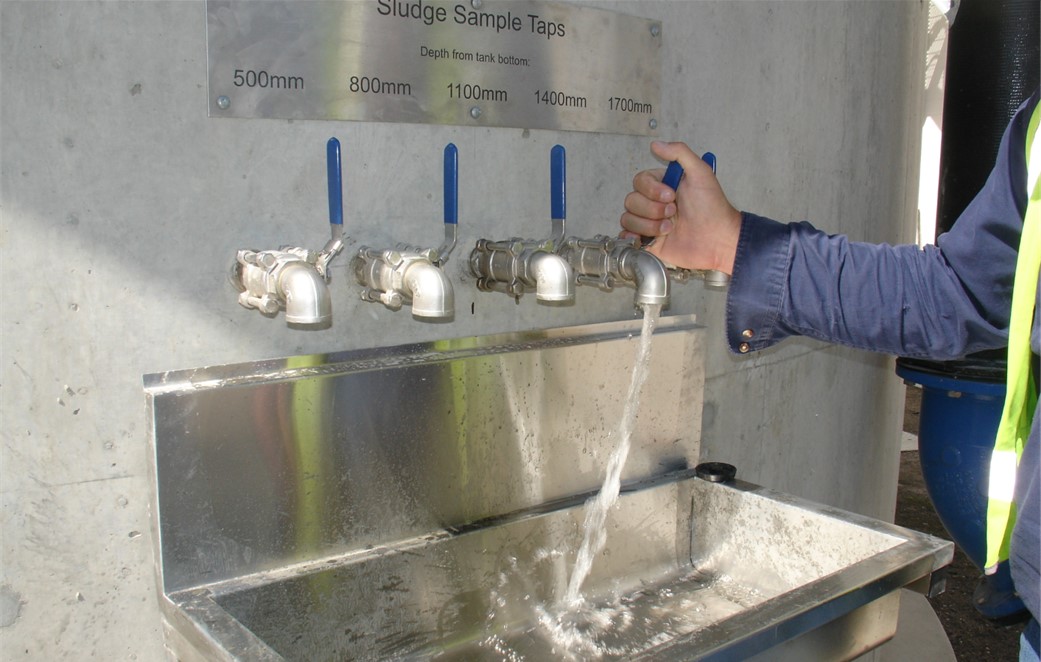
Key benefits of the VeeMax® include:
- Proven heavy duty sludge removal system, suited for thickened sludge.
- Heavy duty gearbox with high service factor.
- Suspended scraper mechanism means less maintenance on the rubber squeegees.
Item | Value |
No. of Units | 1 x 6.5M diameter |
Scraper Type | VeeMax® |
Drive | Centre Drive |
Application | Backwash water |
Launder | 316SS V-Notch |