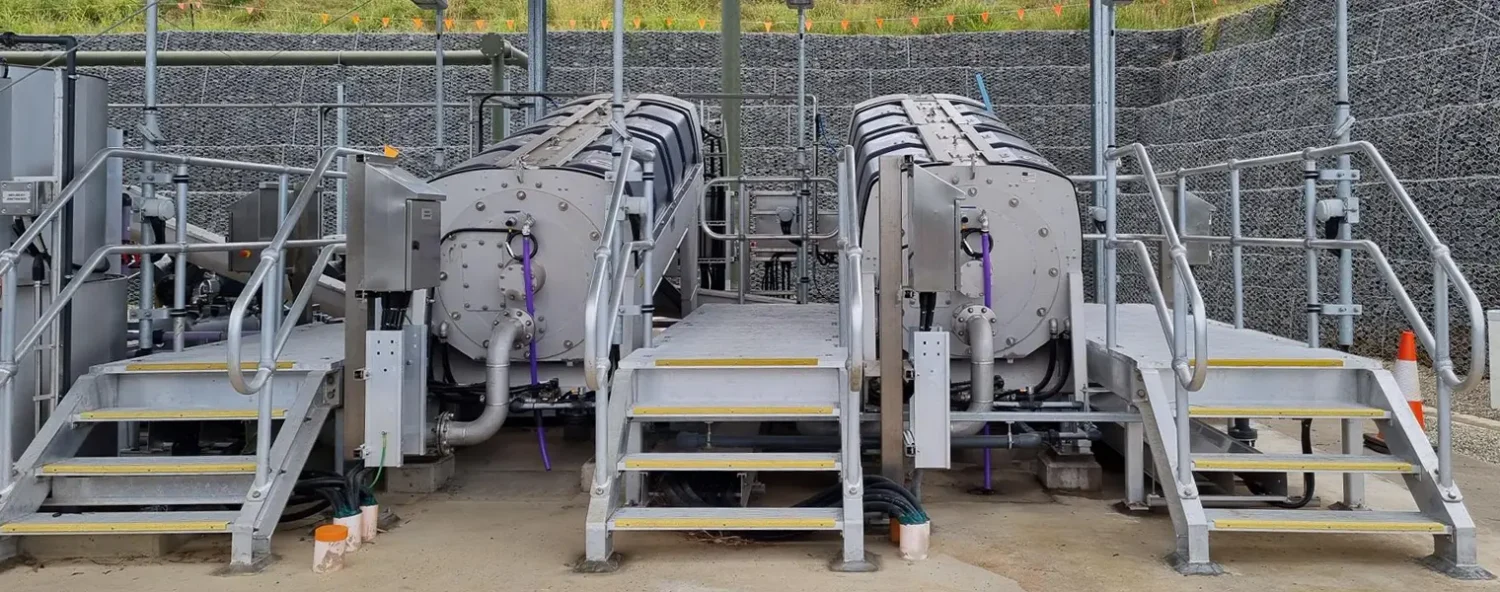
Screw Press
Hydroflux is proud to be Australia’s first water treatment and technology company to achieve Climate Active carbon neutral certification for our entire organization. As part of our climate change mission, we continue to research, develop and invest in sustainable technologies.
Now our journey continues – our main range of water technology and associated chemical products are Climate Active certified as carbon neutral. To read more on our journey, click HERE
The HUBER Q-PRESS® RoS3Q Inclined Sludge Press is a unique sludge dewatering machine developed by HUBER over 20 years ago and now over 1200 machines have been installed globally in a wide variety of applications.
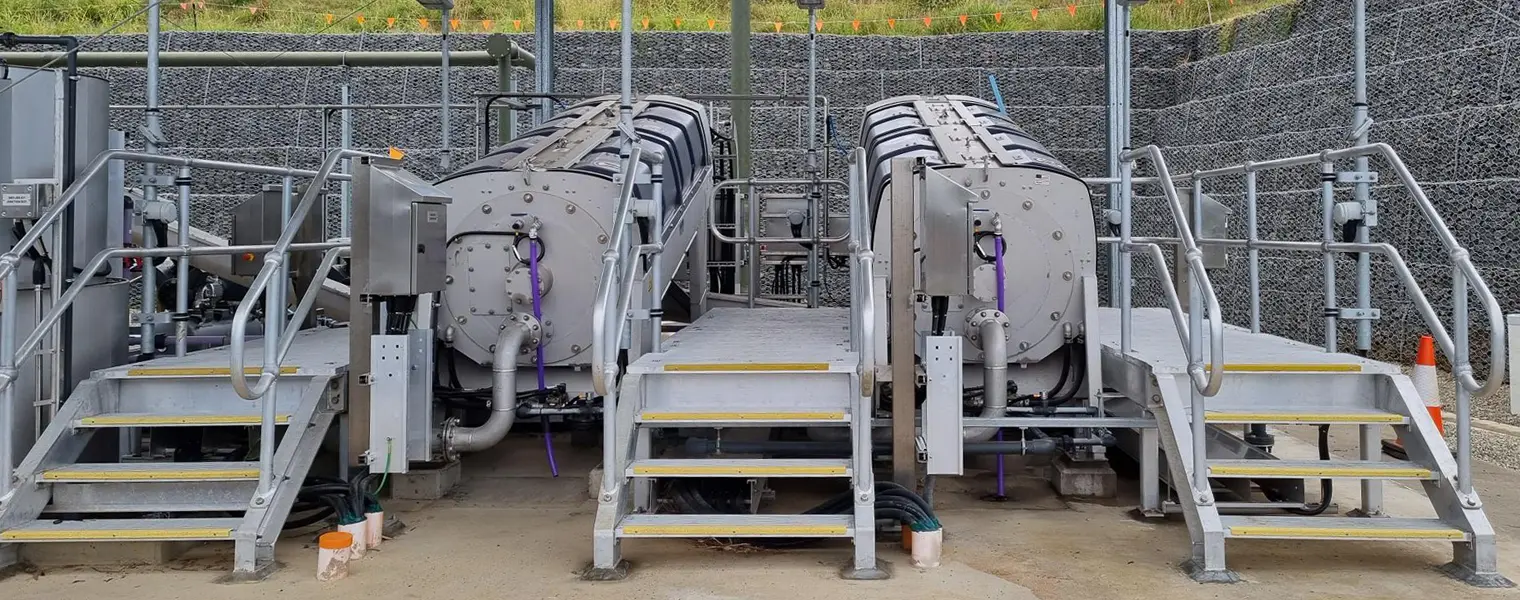
Several HUBER Q-PRESS® models are available with capacities ranging from 20 to 540Kg Dry Solids (DS) per hour to suit virtually all industrial applications for dewatering of primary or secondary sludge.
Some of the key features of the HUBER Q-PRESS® include:
- High performance equivalent to and often better than centrifuges and belt presses
- Very slow speed screw, which prolongs life, with minimal service required
- Very low energy requirement compared to centrifuges
- All stainless steel construction and high quality fabrication in Germany
Find out more
Principle of operation
Sludge is typically transferred to a mixed storage tank or pumped directly from the wastewater treatment plant before being flocculated in-line with a polyelectrolyte and entering the machine.
The machine consists of a main case, internal screw rotating at <1.5rpm, spray bar and cylindrical wedgewire/mesh drum. As the sludge enters the unit the sludge is conveyed by the screw through the drum length whilst the filtrate is drained through the mesh. The drum consists of variable apertures and profiles, and together with a reducing screw pitch and increased shaft diameter, pressure is gradually applied to the sludge mass as it travels up the drum.
An adjustable pneumatic cone is configured to set the pressure at the outlet to optimise the operation of the unit and achieve maximum sludge dryness.
The cake is discharged through the cone into a bin or conveyor system and the filtrate that collects within the main case is discharged via gravity to the filtrate outlet flange.
Capacities
There are currently 4 models in the Huber screw press ranging in capacity to process a dry solids load from 90 kg/hr to 540 kg/hr.
The table below shows the nominal design capacities of the models available
Model Number | Max Hydraulic flow (m³/h)* | Max solids load (kg/h) |
RoS3Q280 | 2 | 90 |
RoS3Q440.2 | 4 | 180 |
RoS3Q620.2 | 10 | 350 |
RoS3Q800.2 | 20 | 540 |
Configurations
There are many ways in which a screw press dewatering plant can be configured which mostly depends on logistics and how the dewatered solids will be removed from site.
A design incorporating a Q620 unit is suitable for generating 20 tons of dewatered cake per day. In this case, it was determined that the most appropriate method due to available space and logistics was to elevate the screw press and construct a conveying system that allows the cake to be discharged across one of two adjacent skip bins below.
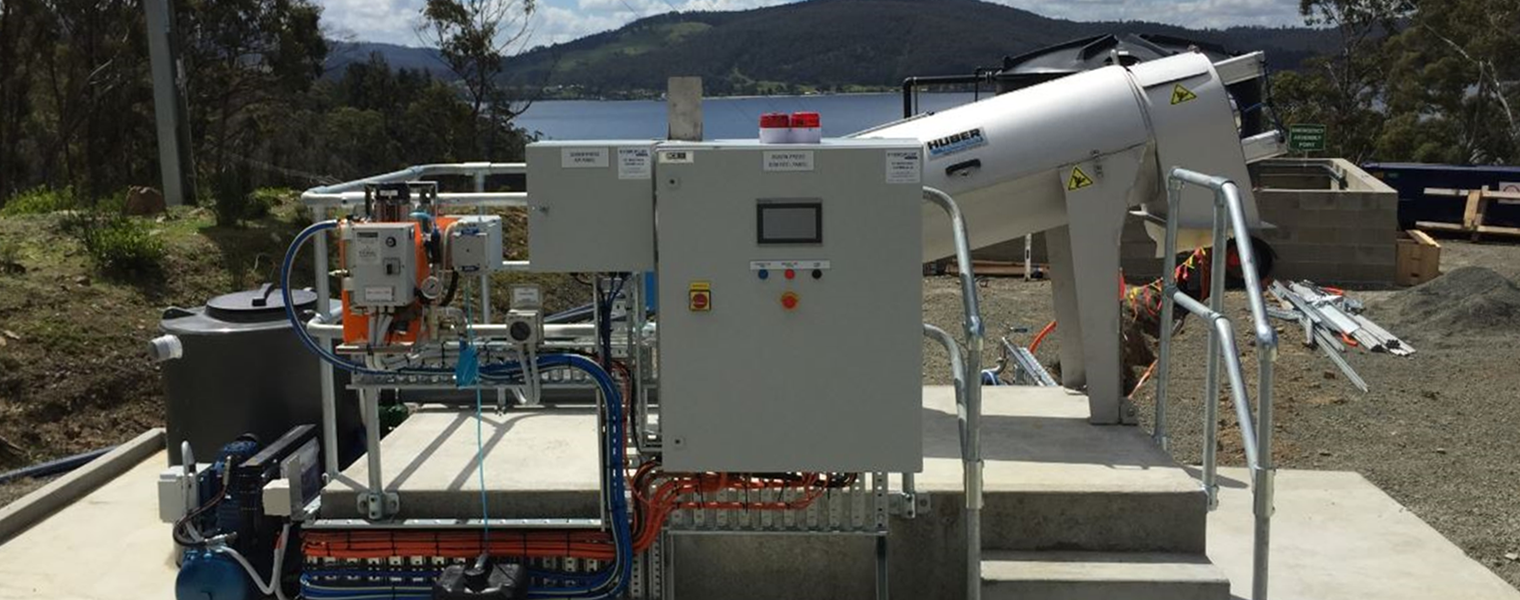
The photograph above shows a small screw press designed to dewater waste activated sludge from an aerobic pond. As the volume of cake that was generated is fairly low, the system was slightly elevated to allow a small forkliftable bin to be placed under the outlet.
Maintenance
The HUBER screw press is designed to require minimal maintenance and typically only once every few years access to the internal screw is required. The latest range of larger machines offers a spilt basket to simplify access to the internal components without the need to remove the main screw.
The following diagrams show the top half of the basket being removed for screw wiper replacement in situ.
Removal of covers & Removal of upper basket –Watch video animation
Periodic maintenance of the screw press is minimal and regular service involves basic cleaning, oil changes and lubrication and can easily be accomplished by in-house personnel.
Hydroflux employs qualified civil, mechanical, chemical and electrical engineers plus a team of experienced project managers, site supervisors, commissioning engineers and service technicians based in offices in most capital cities providing a local presence throughout the duration of the project.
All projects are conducted under externally approved occupational health and safety, and environmental management systems.
Hydroflux is Australia’s first Water-tech company to achieve Climate Active certifications which means his means you are engaging with a carbon neutral organisation without increasing your carbon footprint and you are supporting positive and verified action on climate change.
Hydroflux can complete all the following works in house which are typically required to construct a wastewater treatment plant.
- Process design, development of PID’s and HAZOPS reviews
- Establishment of the most suitable wastewater treatment plant layout
- Equipment and component selection
- Civil and building designs including preparation of documentation for council or other regulators
- Electrical design and programming
- Project management and site supervision
- Environmental / Occupational health and safety plans and report
- Quality assurance plans
- Earthworks, civil works, building works, mechanical and electrical installation
- Commissioning, training and documentation as required.
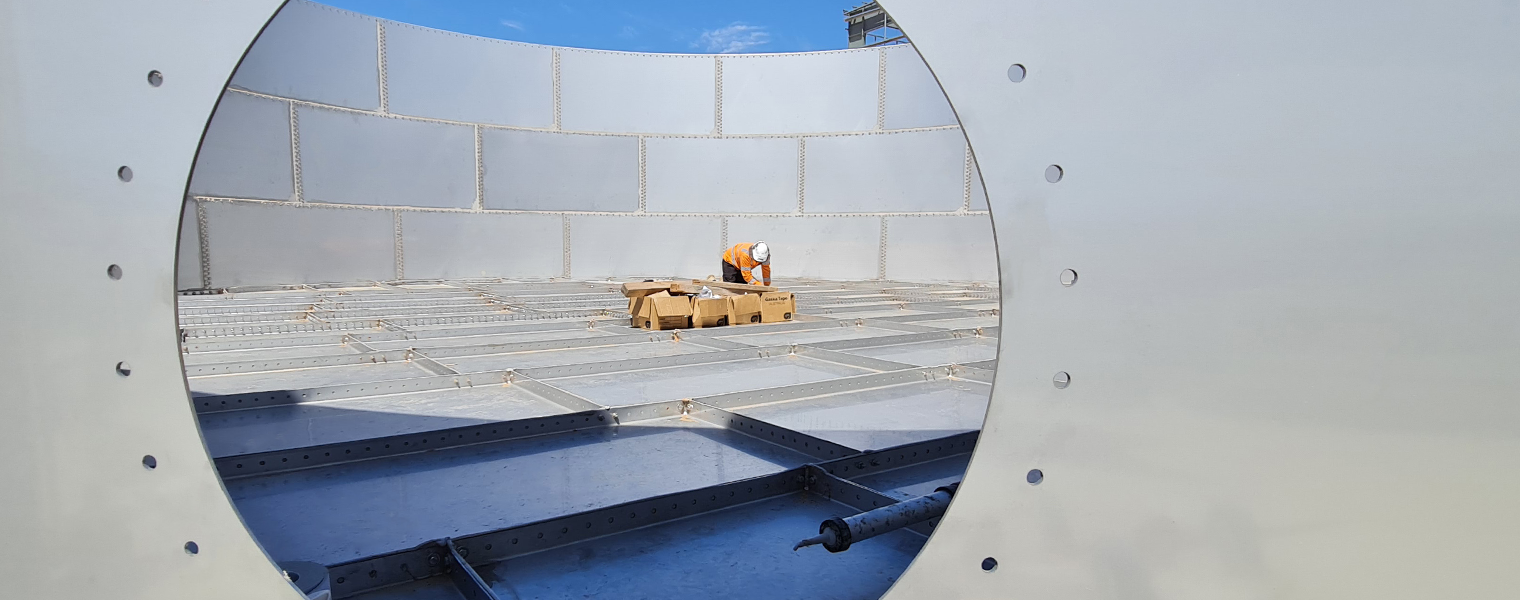
Stainless steel panel tanks are often used for aeration tanks.
